宅配ドライ事業
宅配トドック取扱商品を組合員様のご注文別に仕分けし
全道の宅配センター・デポにお届けします
宅配入庫
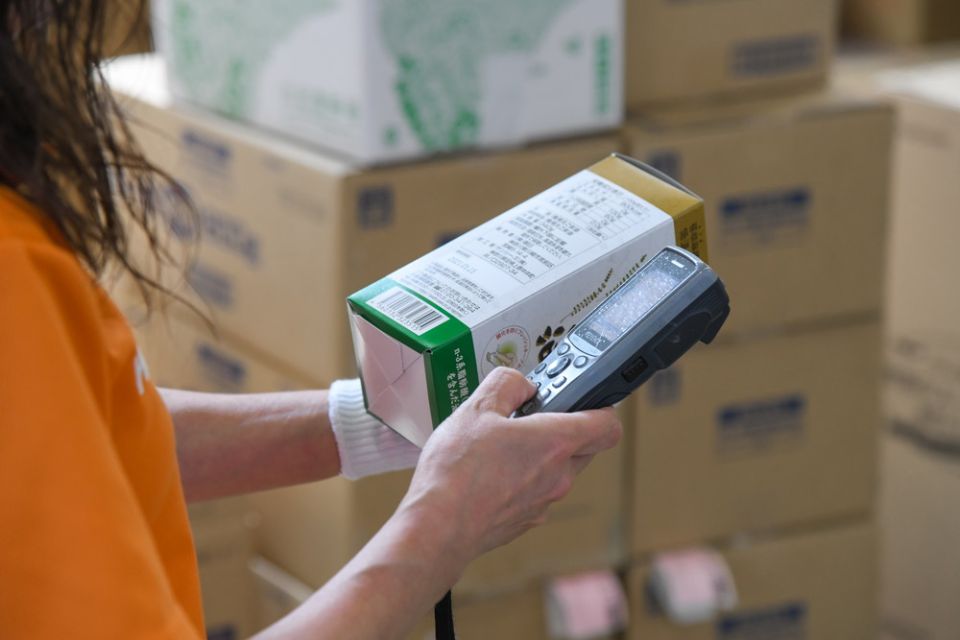
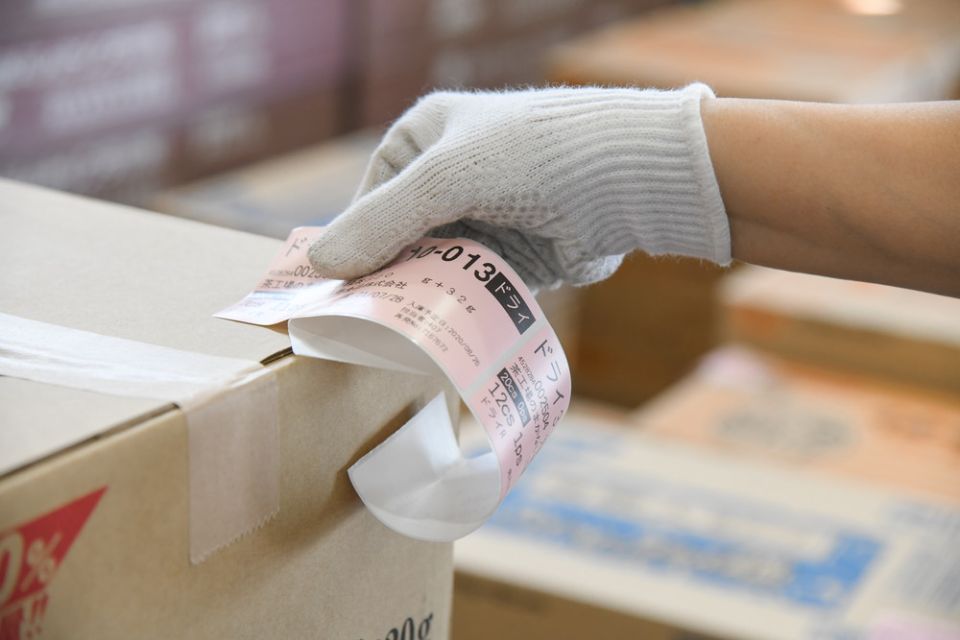
入荷した商品の検収
お取引先様から納品された商品の種類・数量が合っているかチェックし、商品を保管する場所ごとにシールを貼って振り分けます。1日平均約15,000点もの商品が大量に納品されるため、一時保管場所へフォークリフトにより保管します。宅配部門にいるフォークリフト作業者は「入庫」をメインに仕事をしています。
オートストア
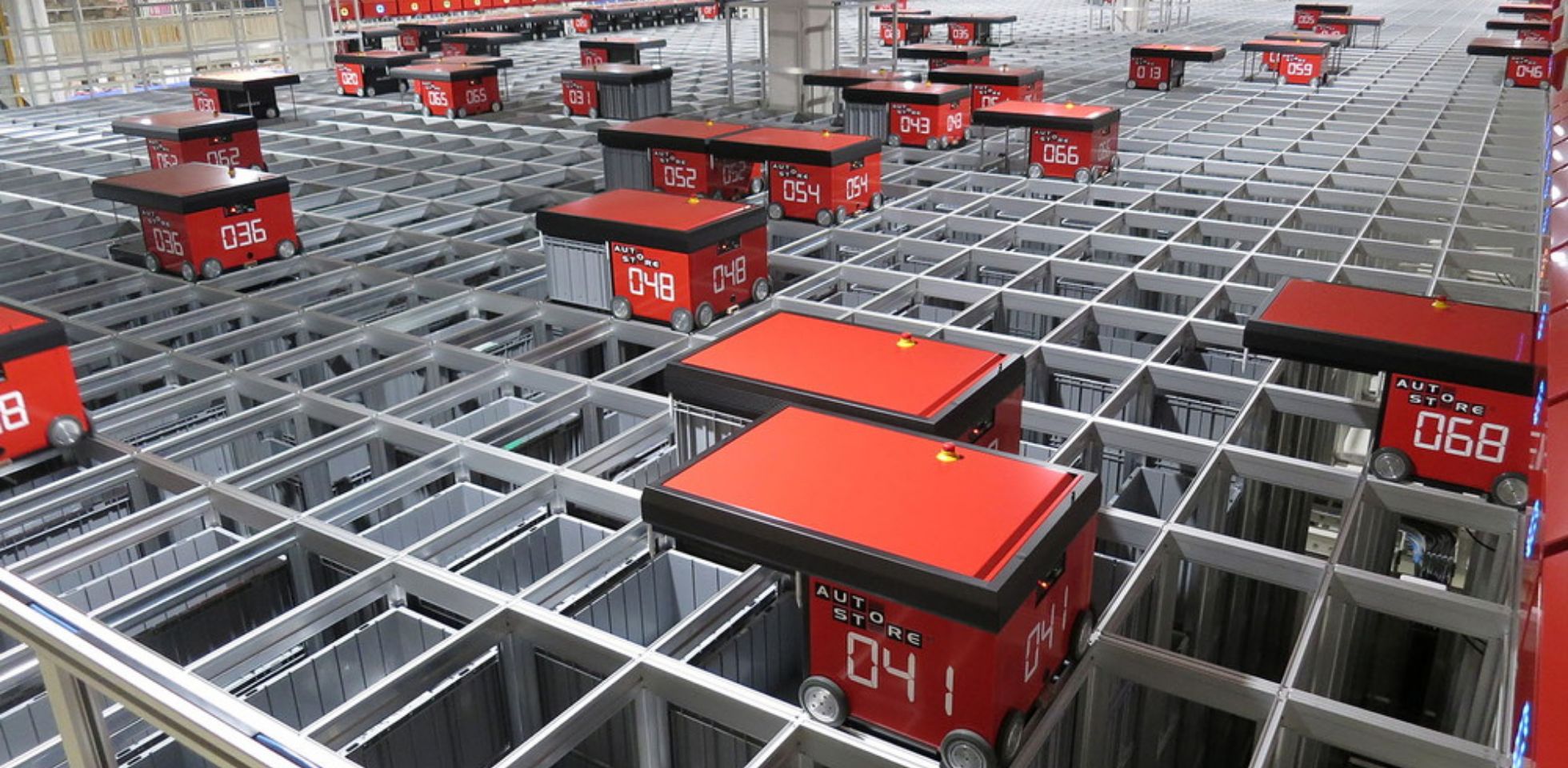
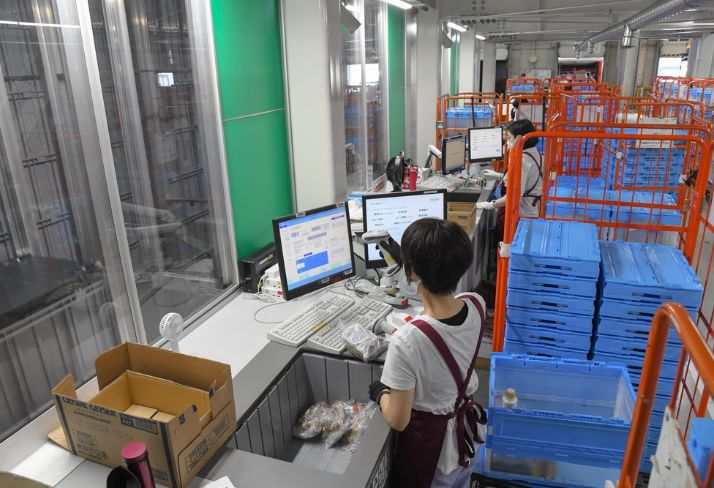
ドライ(食品)、特企(食品以外)の低頻度の商品を格納
売れる頻度が低い商品を、オートストアに格納させます。
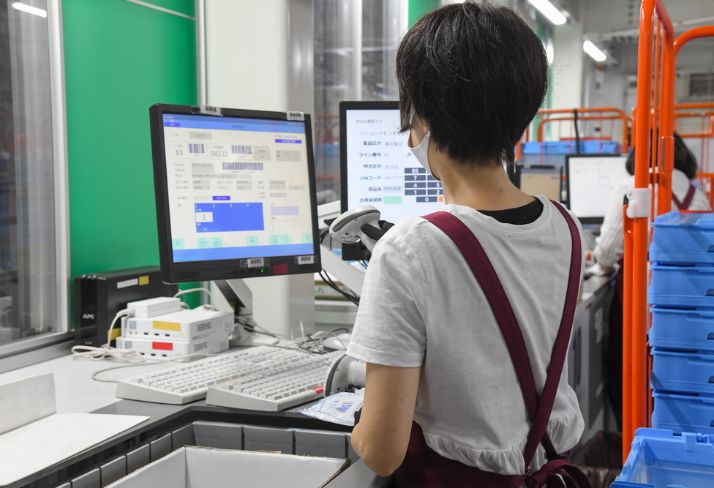
オートストアへの入庫・出庫作業
商品を入庫させるポート(操作窓口)と出庫させるポートが分かれています。午前中ピッキングラインが稼働してからは出庫をメインに、納品が多くなる午後~夕方は入庫をメインに稼働させます。
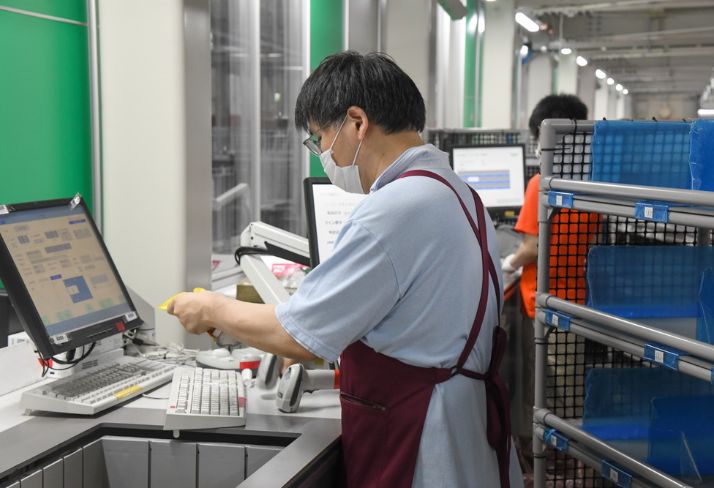
操作はすべてパソコンを使用
商品の入出庫どちらもポートでの作業がメインです。出庫の際は、仕分けるスペースもシステムが指示を出し、商品棚を探して歩き回る必要もありません。マニュアルが完備されているので、パソコンが苦手な方でもすぐに覚えられます。
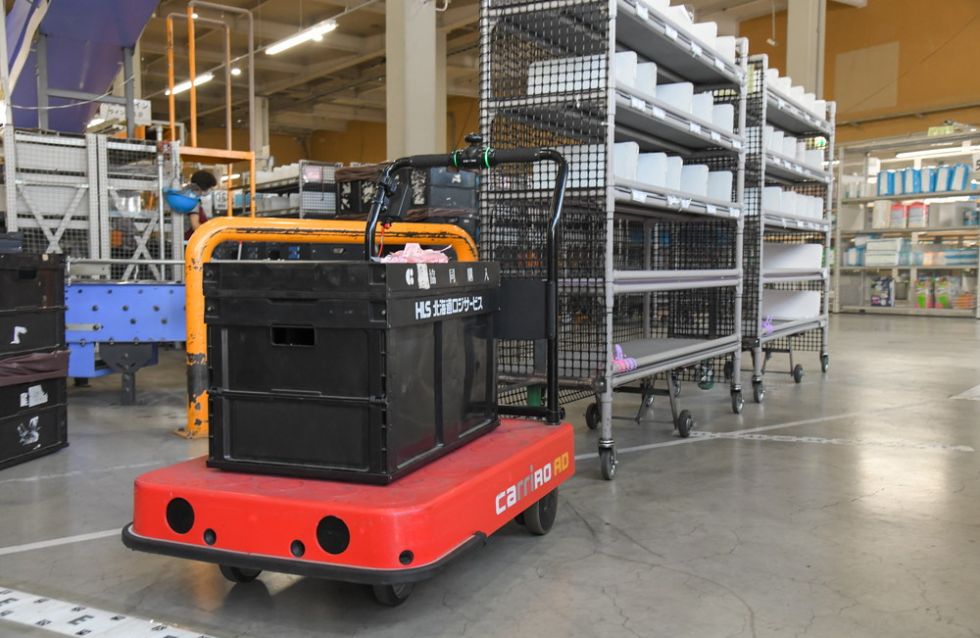
出庫した商品を移動
出庫した商品は、専用カート内にお届け先別で分けて載せ、キャリロ(自律走行型ロボット)を使用して各ラインまで運びます。
キャリロが商品を載せたカートを自動で引っ張るため、重たい荷物を運ぶ必要がありません。
宅配ドライ
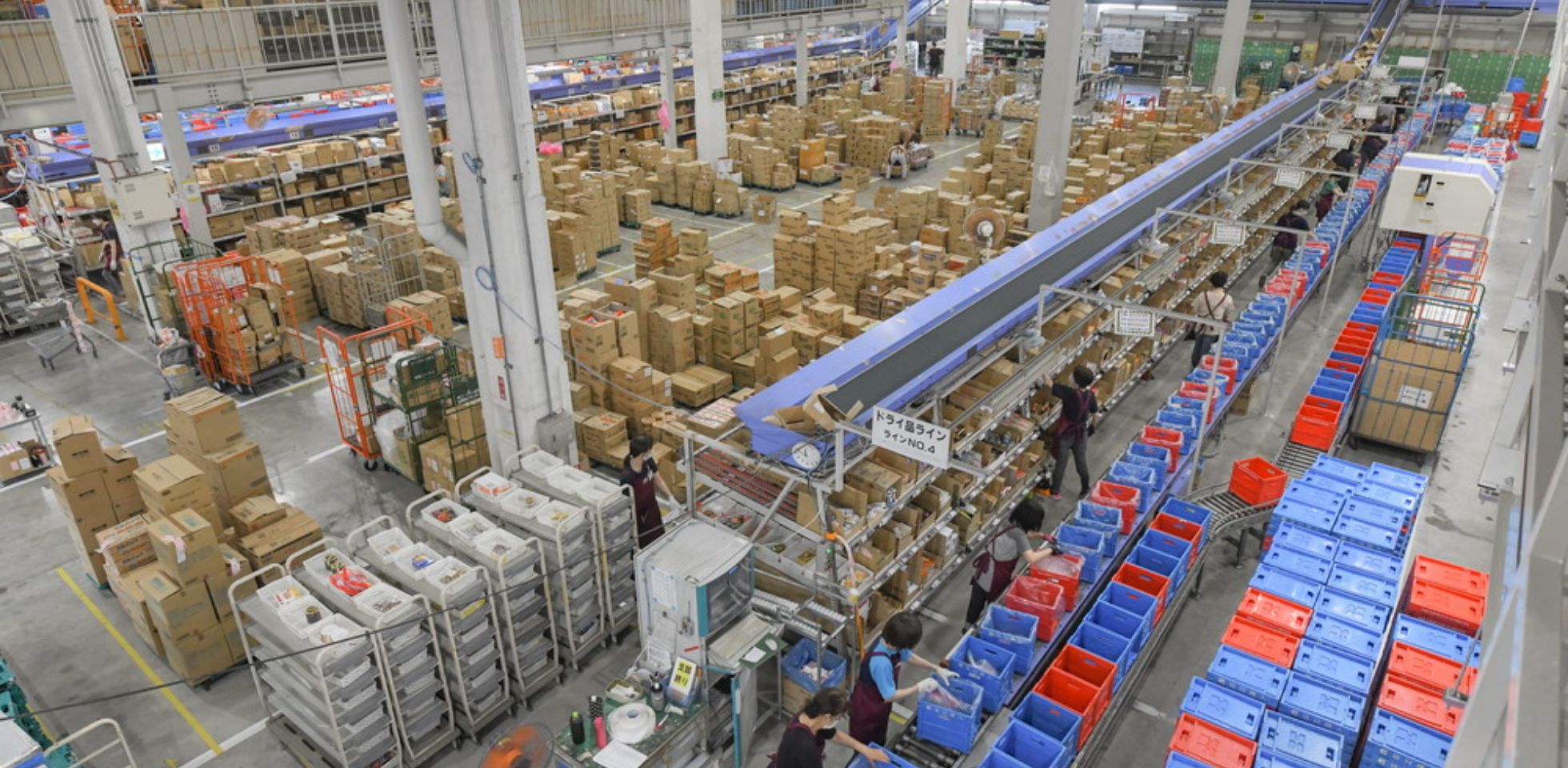
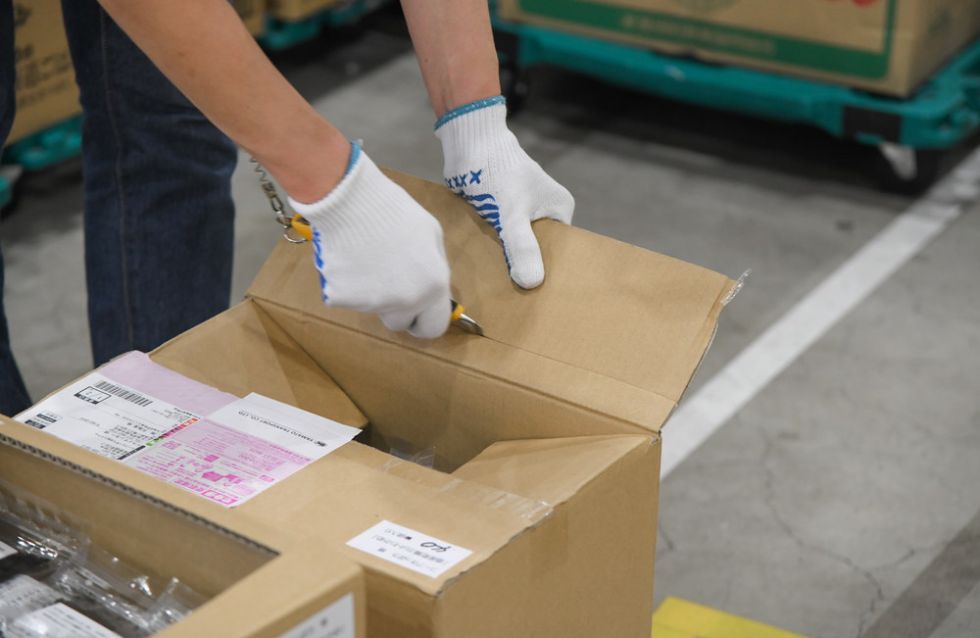
仮置き場での段ボールカット
入庫で検収されたケース(段ボール箱)商品を、バラ(商品1個単位)仕分けできるよう、ケースを開けます。加工されたケース在庫を、入庫時に貼りつけられたシールを基に所定の場所へ移動させます。
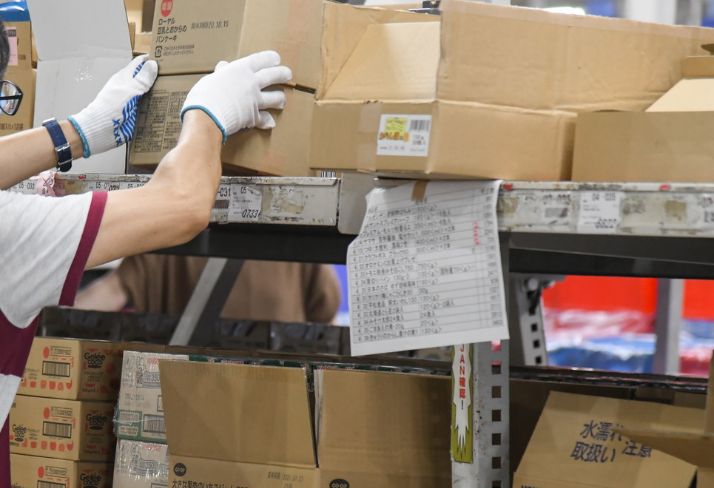
ピッキングライン棚への補充
商品を詰めるピッキングライン作業者が作業できるよう、商品棚に商品を補充します。
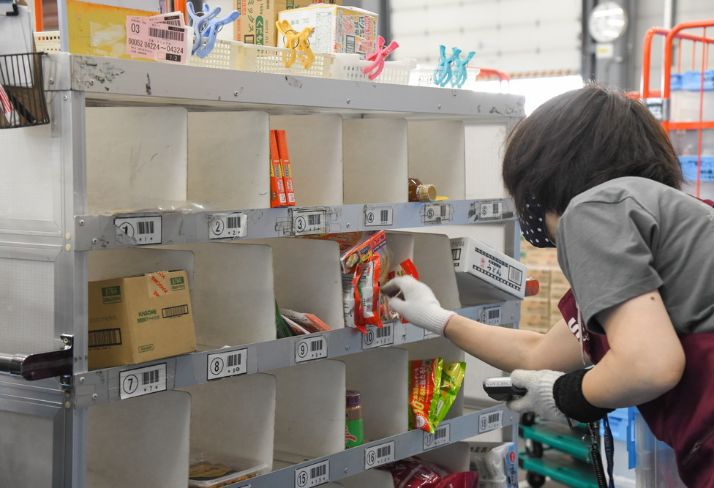
マニュアル(人手)で仕分け
重さや大きさ等の理由でオートストアでは処理できない商品(油や飲料等)が対象です。ここで使われているハンディターミナルは、どの棚からどの商品を集品するかの確認、集品にかかった時間の計測が可能です。
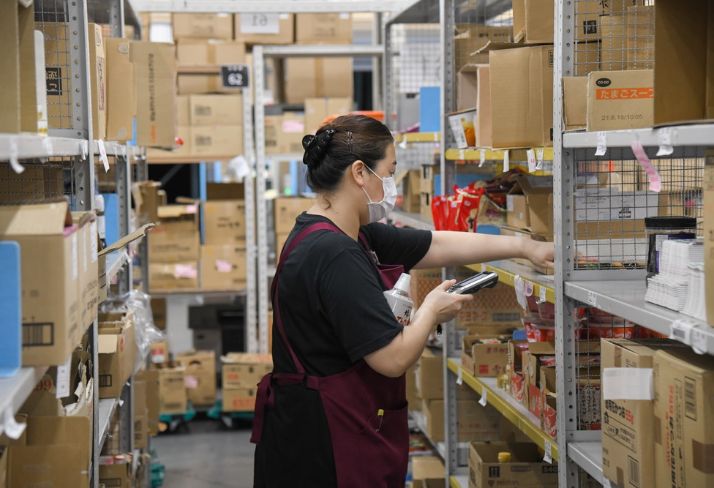
オーダー集品
マニュアルとは別に場所を設けて仕分けをします。こちらもオートストアに入らない商品が対象です。
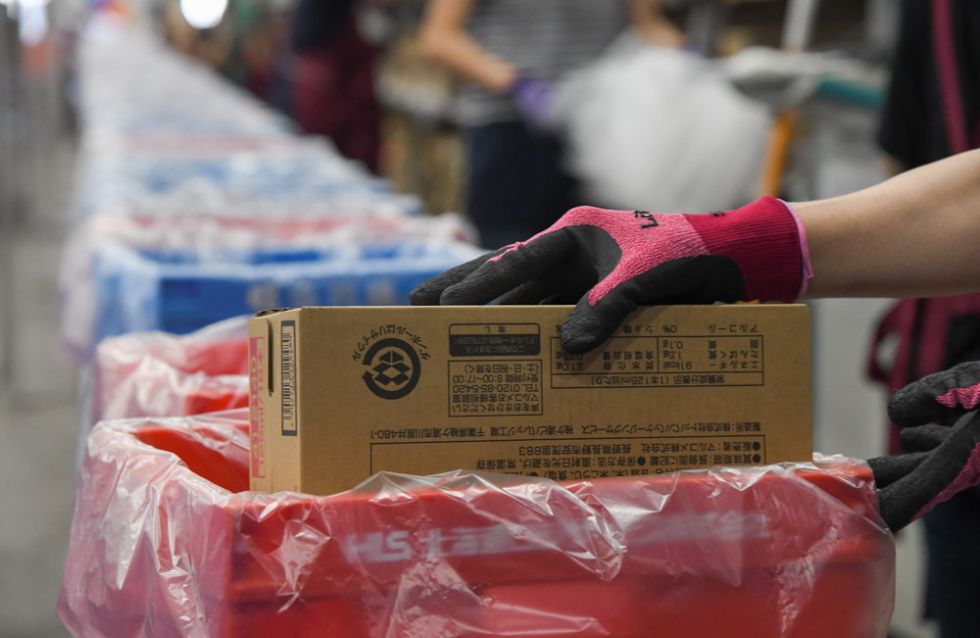
ピッキングラインで
お届け先別に商品を詰める
ピッキングライン上にオリコン(折りたたみ式コンテナ)が流れてくるので、マニュアルで仕分けた商品、商品棚の商品の順で商品を入れていきます。このオリコンはお届け先ごとに分かれており、ここで入れた商品が最終的に組合員様の手元に届きます。当社ではDPSラインを使用しており、生産性向上に貢献しております。
DPSラインとは
DPSライン(デジタルピッキングシステムライン)とはピッキングラインでの支援システムとして導入されました。作業者を配置するゾーンを1列最大16か所設定可能。ゾーンごとに在庫する商品が違い、流れてくるオリコンによって対象・非対象が分かれます。対象のオリコンが近づくとライン上のガイドランプが点灯し、商品棚に設置されている表示器に数量が表示され、これらの表示に従って仕分けを致します。
1日の最大処理物量は約200,000点。当社のオーダーピッチ(1つの商品をオリコンに入れるのにかかる時間)は約2.5秒です。システムにより仕分けが管理されミスを防ぎます。機械と人の手の融合により生産性・精度の向上を致します。
宅配特企/食品以外のペット用品・
洗剤・化粧品・おむつ・薬
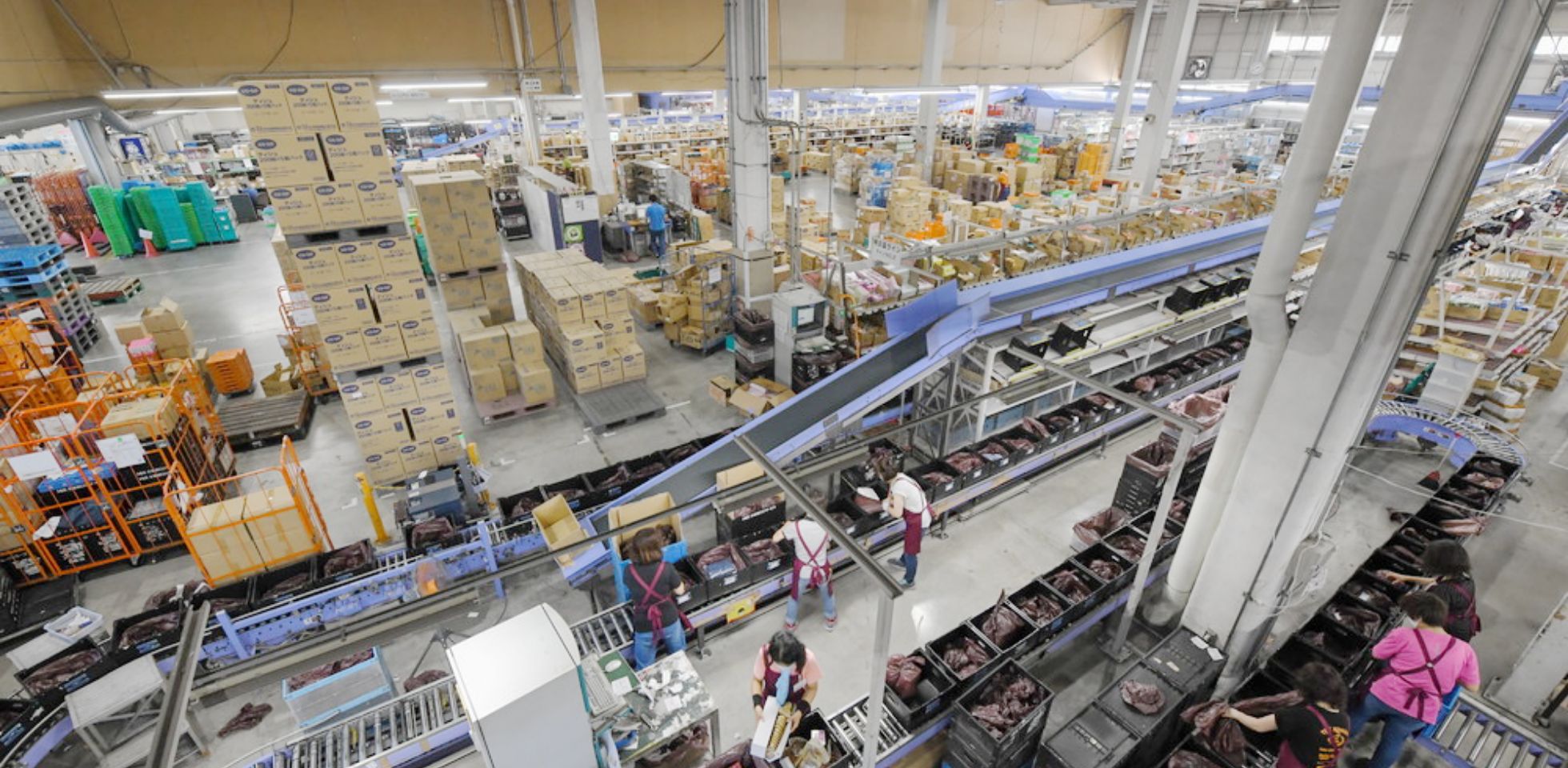
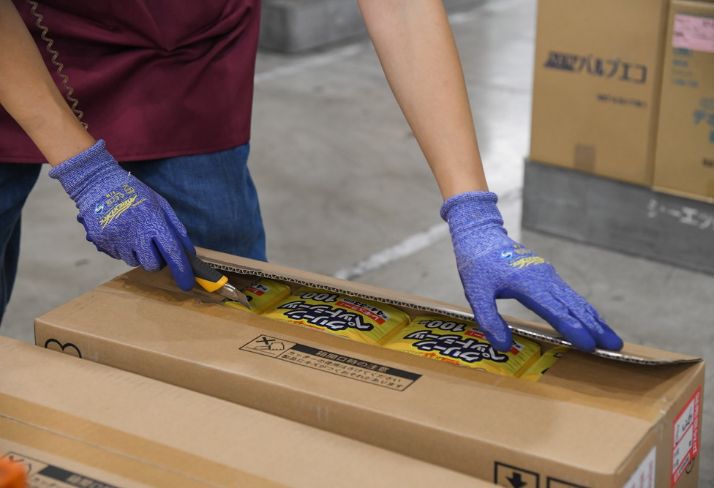
仮置き場での段ボールカット
入庫で検収されたケース(段ボール箱)商品を、バラ(商品1個単位)仕分けできるよう、ケースを開けます。加工されたケース在庫を、入庫時に貼りつけられたシールを基に所定の場所へ移動させます。
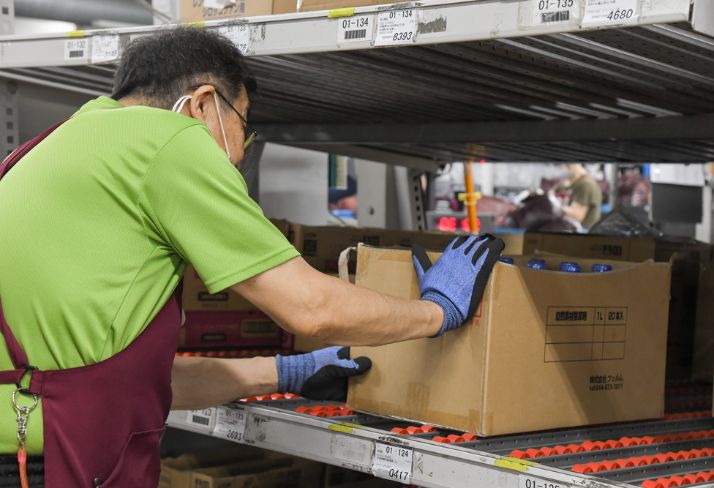
ピッキングライン棚への補充
商品を詰めるピッキングライン作業者が作業できるよう、商品棚に商品を補充します。
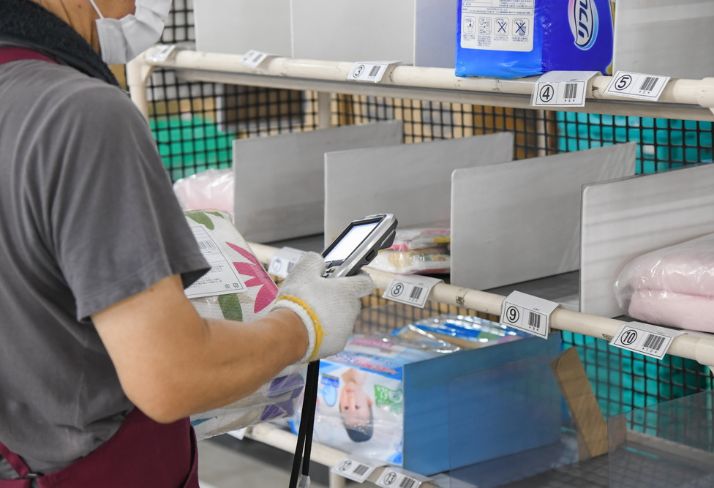
マニュアル(人手)で仕分け
重さや大きさ等の理由でオートストアでは処理できない商品(ペット用品・洗剤・化粧品・おむつ・薬等)が対象です。ここで使われているハンディターミナルは、どの棚からどの商品を集品するかの確認、集品にかかった時間の計測が可能です。
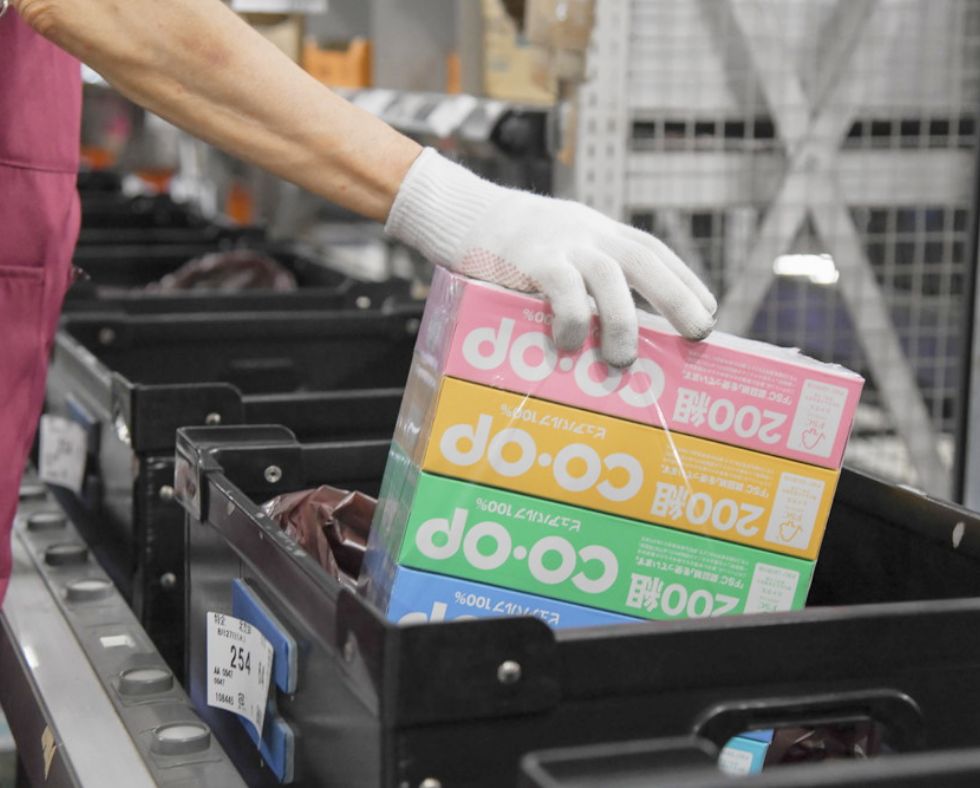
ピッキングラインで
お届け先別に商品を詰める
ピッキングライン上にオリコン(折りたたみ式コンテナ)が流れてくるので、マニュアルで仕分けた商品、商品棚の商品の順で商品を入れていきます。
このオリコンはお届け先ごとに分かれており、ここで入れた商品が最終的に組合員様の手元に届きます。ドライ同様、DPSラインを使用しており、生産性向上に貢献しております。
宅配別積み

センターごとの仕分け作業を実施
専用オリコン(折りたたみ式コンテナ)に入らないケース出荷飲料、酒、卵、米、紙やスコップ等の大型雑貨を、各地域のセンター向けに手で仕分けします。
これらの商品は、各宅配センターに納品後、宅配センター内で組合員様別に仕分けられます。別積みだけで1日あたり約2万5千点の物量を取り扱っております。基本的に大型で重量のある商品が対象ですので、力仕事が多い部門です。
オートストアとは
平置き場の2~3倍の収納力を持つ倉庫の上で、ロボットが自動でピッキングするシステムです。平置き場約600坪・中量棚約250本分の在庫を、229坪に収めることができ、作業人数を約40%削減できます。商品を入れるビン(コンテナ)は13,594個。ロボットは連続20時間稼働でき、走行速度180m/分、昇降速度94m/分。充電率を自ら判断し充電ステーションへ向かいます。北海道では初の導入事例であり、スーパーマーケット事業では国内初の導入です。また、ロボット稼働面積229坪に対しオートストア出庫生産1,900CS/Hは全世界で最大スペックです。作業者は歩き回ることなく商品を手にすることができ、在庫位置の把握も不要。省人化・省力化を実現します。